Metal fabrication plays a vital role in the manufacturing industry, producing essential parts and structures for sectors like construction, automotive, aerospace, and consumer goods. However, this process is not without its challenges. Fabricators face a range of problems, including material wastage, slow production speeds, poor precision, and high labor costs, all of which can negatively impact productivity and profitability.
To remain competitive and meet increasing customer demands, metal fabricators need to adopt advanced solutions that address these common challenges. One of the most significant innovations in recent years is the sheet metal laser cutting machine. Offering a precise, fast, and flexible approach to cutting metals, laser cutting technology has revolutionized the metal fabrication process. This blog explores the problems faced by metal fabricators and how sheet metal laser cutting machines can effectively solve them.
Common Challenges in Metal Fabrication
1. Material Waste
One of the primary concerns in metal fabrication is the amount of material wasted during the cutting process. Traditional cutting methods, such as mechanical sawing or plasma cutting, often result in inefficient material usage due to less precise cutting and higher kerf (cutting width). Material waste can quickly add up, leading to increased costs for fabricators.
2. Low Precision and Inconsistent Quality
In metal fabrication, especially for industries like aerospace or automotive where exact tolerances are crucial, precision is everything. Traditional cutting methods can struggle to maintain high levels of accuracy, especially when working with complex geometries or thin sheet metals. Inconsistent quality can lead to rework, scrap parts, and customer dissatisfaction, all of which negatively affect a business’s bottom line.
3. Slow Production Speeds
Time is money in manufacturing. Traditional metal cutting processes can be slow, especially when working with thicker materials or intricate designs. Manual cutting methods also require more setup time and labor, further slowing down production. In industries with tight deadlines, delays can lead to lost contracts or penalties.
4. High Labor and Maintenance Costs
Many traditional metal cutting methods require skilled operators to ensure precision and efficiency. The reliance on manual labor not only increases costs but also introduces the potential for human error. Additionally, older cutting machines often require frequent maintenance, leading to costly downtime and repair expenses.
5. Limited Flexibility
Traditional cutting methods may lack the flexibility needed to handle different metals, thicknesses, or designs. This lack of versatility can be a significant disadvantage in a competitive industry where customers demand customized products and quick turnaround times.
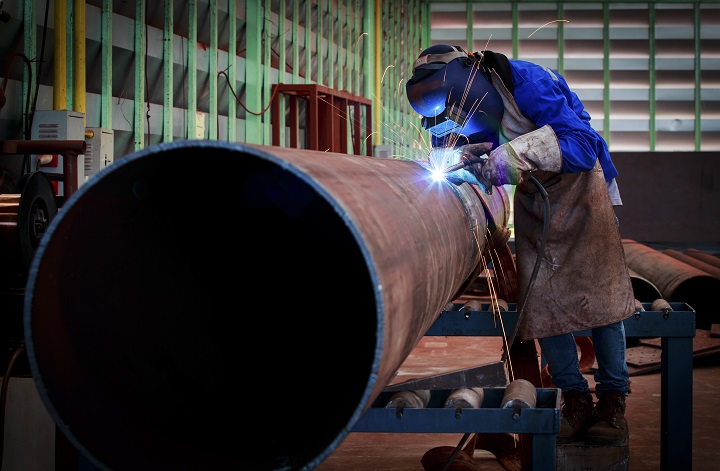
How Sheet Metal Laser Cutting Machines Solve These Problems
Sheet metal laser cutting machines address many of the key challenges faced by metal fabricators. Using a highly focused laser beam to cut through materials, these machines provide a level of precision, speed, and efficiency that traditional methods struggle to match.
1. Reducing Material Waste
Laser cutting machines are known for their high precision and narrow kerf, which significantly reduces material waste compared to traditional methods. The laser beam melts or vaporizes the material along a very thin line, resulting in minimal waste. The ability to nest parts closely together on a sheet maximizes material usage, which can lead to substantial cost savings for fabricators.
Additionally, laser cutting technology minimizes the heat-affected zone (HAZ) around the cut, preserving the integrity of the surrounding material. This feature is especially important when working with metals prone to warping or deformation from heat, such as aluminum or stainless steel.
2. Enhancing Precision and Consistency
One of the standout features of laser cutting machines is their unparalleled precision. The laser can cut with an accuracy of less than a millimeter, which is crucial for industries that demand exact tolerances. This precision ensures that each part is cut to the exact specifications, eliminating the need for rework and reducing the amount of scrap produced.
Moreover, the automation capabilities of laser cutting machines mean that cuts are consistent, regardless of how many pieces are produced. This consistency is essential for mass production and ensures that every part meets the same high standards of quality.
3. Increasing Production Speeds
Laser cutting machines are much faster than traditional cutting methods, especially when dealing with thin sheet metal. The laser can move at high speeds across the material, cutting complex shapes in a fraction of the time it would take with mechanical tools. This speed translates into higher productivity and faster turnaround times for fabricators.
Additionally, modern laser cutting machines come with advanced software that allows for quick programming and easy adjustments, reducing setup times and further boosting production efficiency.
4. Lowering Labor and Maintenance Costs
The high level of automation in laser cutting machines means that they require less manual labor to operate. Once programmed, the machine can run autonomously, with minimal intervention needed from operators. This reduces labor costs and minimizes the risk of human error, leading to more consistent output.
Laser cutting machines also have fewer moving parts than traditional cutting equipment, which results in lower maintenance costs. The lack of physical contact between the cutting tool and the material reduces wear and tear, leading to fewer breakdowns and longer intervals between maintenance.
5. Providing Flexibility and Versatility
One of the most significant advantages of laser cutting machines is their versatility. These machines can handle a wide range of materials, including carbon steel, stainless steel, aluminum, and titanium, making them suitable for various applications. Whether cutting thin sheet metal or thicker plates, laser machines offer precise control over cutting depth and speed.
Additionally, laser cutting machines are highly adaptable to different designs, from simple cuts to complex geometries. With the ability to quickly switch between jobs and materials, fabricators can meet customer demands for customized products without sacrificing efficiency.
—
Advanced Features of Modern Laser Cutting Machines
Modern metal laser cutting machines come equipped with advanced features that further enhance their capabilities in metal fabrication:

1. Fiber Laser Technology
Fiber lasers are highly efficient and powerful, making them ideal for cutting a wide range of metals, including reflective materials like aluminum and copper. They offer faster cutting speeds, higher precision, and lower energy consumption compared to traditional CO2 lasers.
2. Automated Loading and Unloading
Automation is a critical feature for high-volume production. Many laser cutting machines come with automated loading and unloading systems that streamline the production process and reduce downtime between jobs.
3. Real-Time Monitoring and Diagnostics
Modern laser machines are equipped with sensors and software that monitor the cutting process in real-time. These systems can detect potential issues, such as material inconsistencies or laser misalignment, and make adjustments automatically. This level of control ensures that the machine operates at peak efficiency and reduces the risk of errors.
4. Integration with Industry 4.0
As part of the move toward smart manufacturing, many laser cutting machines can be integrated into digital production environments. This integration allows for real-time data collection, predictive maintenance, and improved workflow management, all of which contribute to higher productivity and reduced downtime.
Conclusion: Laser Cutting Machines as the Solution to Metal Fabrication Challenges
The challenges faced by metal fabricators—material waste, slow production, high costs, and inconsistent quality—can be effectively addressed by adopting Metal laser cutter. These machines offer superior precision, speed, and versatility, making them an indispensable tool for modern metal fabrication.
With the continued advancements in laser cutting technology, fabricators can reduce costs, improve quality, and increase productivity, ensuring they remain competitive in a rapidly evolving industry. Whether you’re a small shop or a large-scale manufacturer, investing in a laser cutting machine can transform your metal fabrication process and set you up for long-term success.